Master Food Safety & Ace Inspections with Jolt
Jolt’s food safety software digitizes checklists, temperature logs, and labeling to ensure compliance, simplify health inspections, and improve your restaurant’s safety standards.
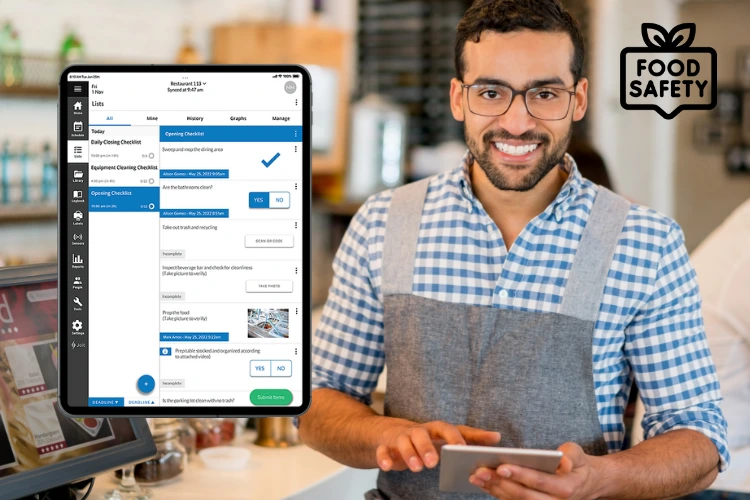
Tired of Food Safety Stress & Paperwork Chaos?
Manual processes and inconsistent follow-through can turn food safety into a constant battle, risking your reputation, compliance, and bottom line.
- Dreading Health Inspections? (Fear of violations, fines, or closures)
- Inconsistent Staff Execution? (Missed checks, pencil-whipping, forgotten tasks)
- Error-Prone Paper Logs? (Illegible, easily lost, hard to audit)
- Compliance Anxiety? (Unsure if you’re meeting all requirements)
- Food Waste & Spoilage? (Due to improper temperature or labeling)
- Reputation on the Line? (Risk of food borne illness outbreaks)
Jolt: Food Safety, Simplified & Systematized
Jolt replaces outdated paper trails and guesswork with a powerful, easy-to-use digital platform. We empower your team to execute food safety protocols perfectly every time, providing managers with real-time visibility and irrefutable digital records.
Lists & Library
Sensors
Probes
Labeling
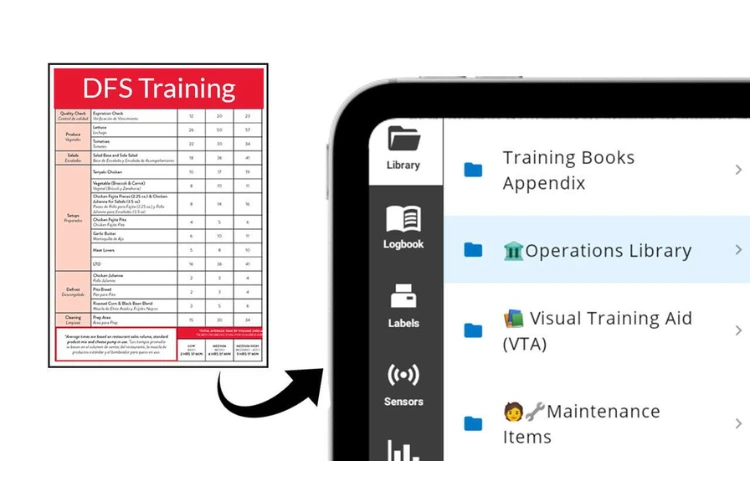
How Jolt Lists & Library Drive Consistency and Compliance
Complementing the power of Jolt Lists is the Jolt Library, information storage of things such as standard operating procedures (SOPs) and training videos. This feature saves managers significant time by providing access to industry best-practice trainings that can be quickly accessed by staff. The Library ensures that teams are working from standardized, up-to-date information. This makes it easy to roll out new procedures across multiple locations consistently, ensuring that all staff adhere to the latest food safety protocols and company standards.
Together, Jolt Lists and the Jolt Library create a robust, documented, and easily auditable food safety system. By leveraging expert-designed templates from the Library and ensuring their consistent execution via digital Lists, businesses can build a strong culture of food safety. This not only helps in preventing foodborne illnesses and protecting the brand’s reputation but also prepares the restaurant for health inspections with a complete, accurate, and readily accessible digital record of all food safety activities, demonstrating proactive compliance and operational excellence.
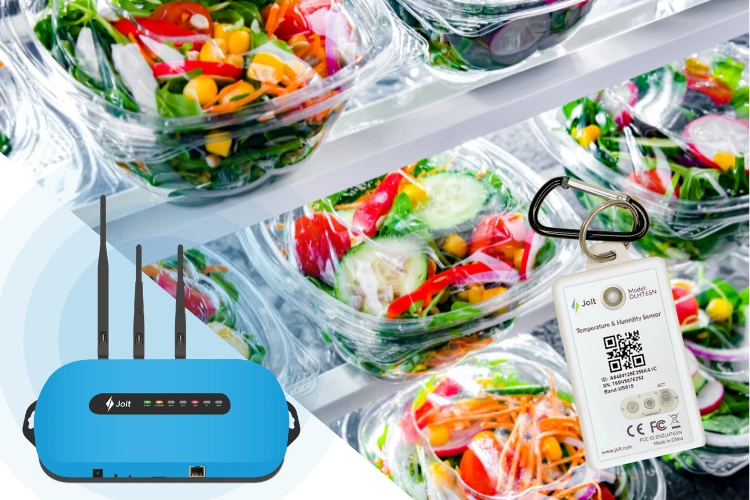
Jolt Sensors Give 24/7 Protection with Real-Time Alerts
The true power of Jolt Sensors in enhancing food safety lies in their intelligent alert system and automated record-keeping. When a sensor detects an out-of-range temperature, it immediately triggers notifications to designated managers or staff via push notifications, text, or email. This allows for swift corrective actions—such as adjusting equipment, investigating a malfunction, or relocating products—before food quality is compromised or items become unsafe for consumption, significantly reducing the risk of foodborne illness and costly spoilage. Furthermore, all temperature readings are automatically logged digitally within the Jolt platform, creating an accurate, tamper-proof, and easily accessible record for internal audits, troubleshooting, and demonstrating due diligence during health inspections, ensuring compliance becomes effortless.
Ultimately, by automating a critical control point, Jolt Sensors give businesses unparalleled peace of mind and control over their food safety environment. They transform temperature monitoring from a reactive, often burdensome task into a proactive, data-driven process. This not only helps in safeguarding public health and protecting the brand’s reputation but also contributes to operational efficiency by minimizing food waste and freeing up staff from tedious manual logging, allowing them to focus on other important tasks.
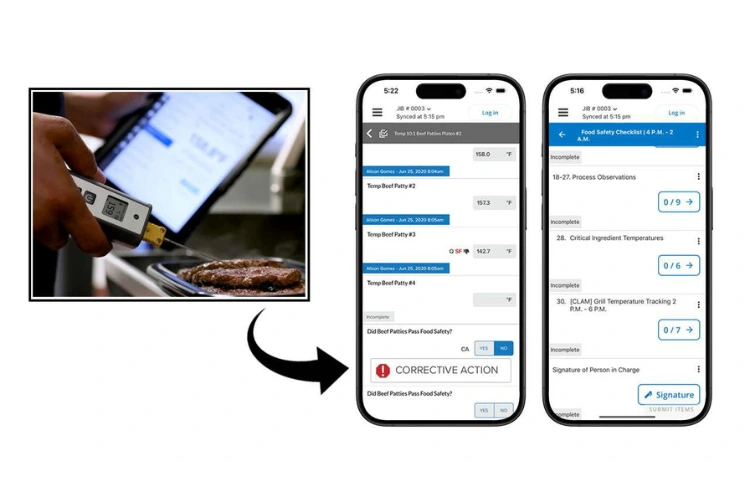
Jolt Probes for Verifiable Food Safety & Compliance
The real advantage for food safety comes from the seamless integration of these probe readings into Jolt’s comprehensive digital record-keeping system. Each temperature taken is automatically time-stamped and logged against the specific food item or task, creating an irrefutable audit trail. This provides managers with real-time visibility into temperature compliance and allows for immediate corrective actions if a reading falls outside safe parameters. For health inspections, this means having organized, accurate, and easily searchable temperature logs at your fingertips, demonstrating due diligence and a robust commitment to food safety protocols. This accountability and traceability are crucial for identifying potential issues early and maintaining high safety standards.
By digitizing and streamlining the essential task of temperature taking, Jolt Probes empower employees to perform their food safety duties more efficiently and accurately. This not only reduces the risk of serving unsafe food but also instills a stronger culture of food safety within the organization. The ease of use, coupled with the robust data capture, ensures that businesses can confidently manage one of the most critical elements of their HACCP plan, protecting both their customers and their reputation.
Eliminate Labeling Errors & Boost Compliance with Jolt
This meticulous approach to labeling directly supports essential food safety practices like First-In, First-Out (FIFO) stock rotation, drastically minimizing the chance of using expired or spoiled ingredients. Clear, unmistakable date codes and item identifiers mean staff can quickly assess product freshness and make informed decisions, reducing food waste and, more importantly, safeguarding consumers from potential foodborne illnesses. Furthermore, prominent allergen labeling, made easy with Jolt’s customizable templates, is vital for protecting customers with sensitivities and ensuring compliance with allergen management regulations.
During health inspections, Jolt’s consistent and accurate digital labels provide tangible proof of a robust food safety program. Inspectors can easily verify that products are correctly dated, rotated, and that allergen information is clearly communicated. This demonstrates a commitment to detail and proactive safety measures, contributing to better inspection outcomes and reinforcing the restaurant’s reputation for prioritizing food safety and consumer well-being.
With Jolt, You Don’t Just Do Food Safety – You Master It.
Pass Health Inspections with Confidence
Walk into audits prepared with easily accessible, irrefutable digital records. Demonstrate proactive compliance and impress inspectors.
Ensure Rock-Solid Compliance
Automate record-keeping and standardize procedures to meet and exceed HACCP, FDA, and local health department requirements.
Boost Staff Accountability & Consistency
Clear assignments, time-stamped completions, and photo verification ensure tasks are done right, by the right person, at the right time.
Prevent Food Borne Illness
Proactive temperature alerts and consistent critical control point checks minimize risks, safeguarding your customers and reputation.
Reduce Costly Food Waste
Accurate temperature monitoring and precise date labeling prevent spoilage and ensure proper stock rotation.
Save Time & Eliminate Paperwork
Free up valuable staff and manager time by digitizing manual logs and reporting.
Turn Health Inspections from Stressful to Successful
How would it be if your next inspection didn’t have frantic searching for paper logs and no questioning if tasks were done. Jolt provides a complete, organized digital trail of all your food safety activities – from temperature logs and corrective actions to completed cleaning schedules. Inspectors appreciate the transparency and accuracy, leading to smoother audits and better scores.
- Instant access to digital temperature logs
- Time-stamped checklist completion with photo/signature verification
- Documented corrective actions
- Easy-to-search historical data
Businesses Using with Jolt
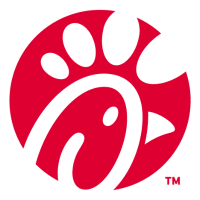
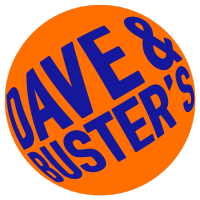
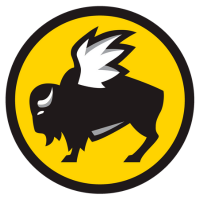
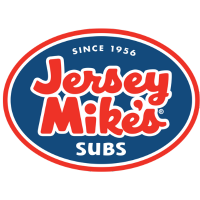
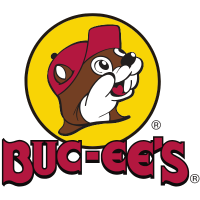
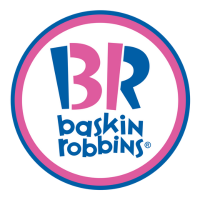
Our store recently got an evaluation from EcoSure and we received a Pride Award. The person doing the inspection said it was the cleanest Dairy Queen store they had ever seen.
Devra C.
Dairy Queen Franchisee
Jolt makes it easy to have accountability and a good follow up process if things aren’t being done the way people are asked to do them.
Jamie S.
LEGOLAND Ops & Compliance
Since implementing Jolt three years ago we have seen an increase in our inspection scores across all of our locations. Furthermore, Jolt has saved us thousands and thousands of dollars from failed audits, labor costs, failed freezer units going out, and so much more.
Chad L.
Zaxby’s Operator